Reverse osmosis equipment water production abnormalities may involve a number of aspects of the problem, including a decline in water production, desalination rate reduction and pressure drop increase. This article is based on several common causes and their solutions summarized from experience.
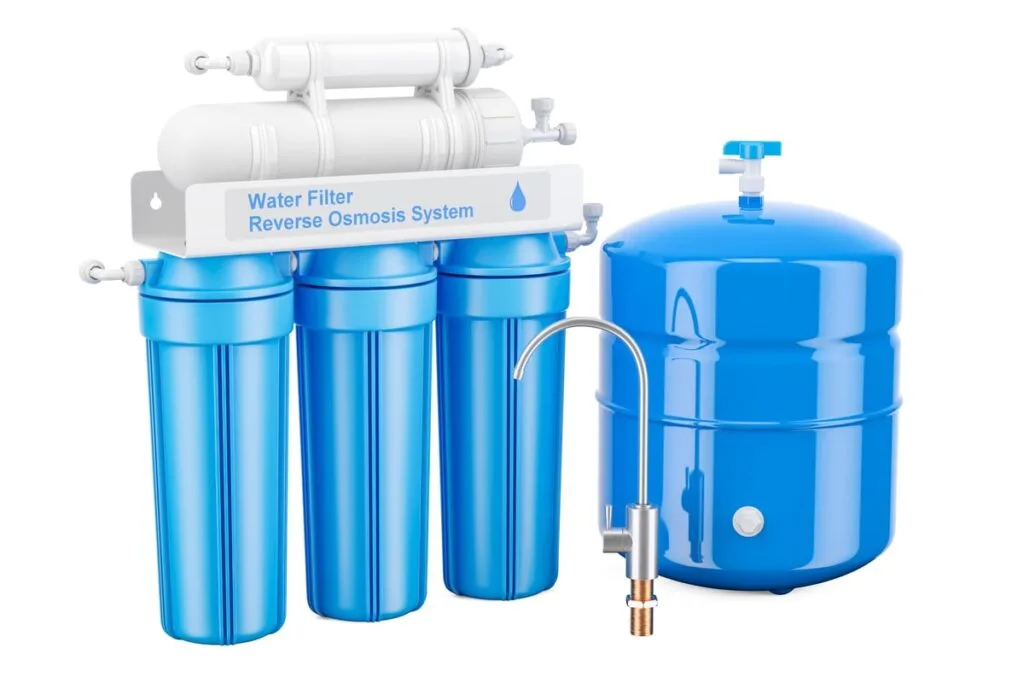
Reverse osmosis equipment water production abnormalities may involve a number of aspects of the problem, including decreased water production, desalination rate reduction and increased pressure drop. The following are several common causes and solutions summarized from experience:
1. Decrease in water production:
- Membrane contamination: particulate contaminants are deposited in the first section of the membrane, fouling contamination exists in the last section, or the whole system is fouled.
- Inlet water temperature is too low: every 3 ℃ lower inlet water temperature, water production is reduced by about 10%.
- Increase in inlet conductivity: High conductivity increases osmotic pressure, resulting in a decrease in water production.
- System design is not reasonable: such as water production side of the pressure is not set properly or piping design is not reasonable, resulting in a reduction in net pressure.
- Membrane element aging or damage: membrane element flux attenuation or by mechanical damage, need to replace the membrane element.
2. Desalination rate is reduced:
- Membrane contamination: Microbial and natural organic contamination may lead to a decrease in desalination rate.
- Chemical damage: the membrane is damaged by oxidizing agents, resulting in a decrease in desalination rate.
- Instrumentation reading error: conductivity meter is not calibrated, resulting in a low calculated desalination rate.
3. Pressure drop increase:
- Irrational design of piping: leading to higher pressure loss.
- Problems of pretreatment system: such as insufficient flocculant dosage, excessive load of multi-media and activated carbon filtration.
4. Other common problems:
- Improper system maintenance: such as improper shutdown protection, wrong dosage of acid or scale inhibitor.
- Instrument calibration problems: pressure gauges, flow meters, etc. are not calibrated, inaccurate readings.
For these problems, corresponding measures should be taken, such as cleaning membrane elements, adjusting operating parameters, improving pretreatment system, regular calibration of instruments, etc., to ensure the normal operation and efficient output of reverse osmosis system.
How to effectively clean reverse osmosis membrane elements to reduce contamination and increase water production?
1. In-situ cleaning: Utilize the medicinal washing water tank, washing water pump and pipeline accompanying the reverse osmosis membrane system to carry out cyclic cleaning or immersion cleaning for the membrane element in the membrane shell. This method does not need to disassemble the membrane element, maintenance workload is small, after cleaning the membrane element can be directly put into use again.
2. Physical Cleaning (Flushing): The membrane element is flushed by physical means without changing the state of the pollutants, and is suitable for preliminary removal of surface pollutants.
3. chemical cleaning: the use of specific chemicals to clean the membrane element, can effectively remove the membrane surface of organic, inorganic and other pollutants. For example, the use of pH 10 of 2% sodium tripolyphosphate solution, 0.8% EDTA tetrasodium (replaced by 0.25% Na-DDBS in severe cases), the temperature of 40 ℃ cleaning solution.
4. Off-line cleaning: the membrane element is removed and cleaned, suitable for severe contamination or the need for deep cleaning.
5. Positive osmosis strategy: the effects of different combinations of cleaning and cleaning time on membrane flux and retention rate based on positive osmosis strategy for reverse osmosis produced water, simulated reverse osmosis concentrated water, and simulated seawater were investigated in order to solve the contamination problem of reverse osmosis membranes in the process of seawater desalination.
6. non-oxidizing biocide immersion: the reverse osmosis membrane element is immersed in a non-oxidizing biocide and then rinsed with a cleaning solution.
7. High-quality water rinsing: after the cleaning chemicals and membrane element circulation, the membrane element should be rinsed with high-quality water that does not contain oxidizing agents such as residual chlorine, and it is recommended to use the produced water of the membrane system.
8. Regular cleaning and maintenance: according to the type and degree of membrane contamination, select the appropriate cleaning agent and cleaning program to ensure that the cleaning is thorough and will not cause damage to the membrane.
9. High-flow produced water rinsing: Use RO produced water to rinse the unit at high flow rate for 15 minutes.
10. low flow rate and low pressure replacement: low flow rate and as low as possible pressure replacement of raw water within the membrane element, the pressure should be low enough not to produce significant permeate water.
11. Low Pressure, Low Flow Rate Input of Cleaning Fluid: Initial cleaning should be done with low pressure, low flow rate input of cleaning fluid, and progressively at pressures so low that no visible permeate water is generated as a guideline.
What is the specific effect of feed water temperature on water production and how is it adjusted in a reverse osmosis system?
In reverse osmosis systems, feed water temperature has a significant effect on water production. According to several lines of evidence, water production increases by 2.5% to 3.0% for every 1°C increase in feed water temperature. This is because as the water temperature increases, the viscosity of the water molecules decreases and their speed of movement increases, thereby increasing the water flux through the membrane.
However, either too low or too high a feed water temperature can adversely affect the system. For example, at lower temperatures, the system may be at risk of freezing and reduced water production. Therefore, when designing and operating a reverse osmosis system, the range of feed water temperatures needs to be considered and appropriate regulation measures taken.
Regulation methods include:
1. raising the feed water temperature: raise the feed water temperature by heating equipment to ensure it is within the appropriate range.
2. using variable frequency pumps: adjust the feed water pressure according to the actual demand, in order to maintain a stable water production.
3. Increase the number of membrane elements: At low temperatures, the reduction in water production can be compensated by increasing the number of membrane elements.
4. temperature-pressure feedback system: some advanced systems use temperature-pressure feedback mechanism, can automatically adjust the inlet pressure to ensure that no matter how the inlet temperature changes, the flow rate of produced water can remain stable.
It is also important to note that while increasing the temperature can increase the water production, it can also lead to a decrease in the desalination rate and an increase in the salt permeability.
What are the early identification methods for aging or damage of membrane elements in reverse osmosis equipment?
1. Abnormally high conductivity: If the salt content (conductivity) of the produced water from a particular series or pressure housing in a reverse osmosis or nanofiltration system is abnormally high, this may indicate leakage of the “O” ring or a failure of the element at that location.
2. Membrane surface abrasion: The front element is often the most susceptible to abrasion from crystals in the source water or suspended metal with sharp edges. Through a microscope to observe the membrane surface can be checked for such damage, once this kind of failure occurs there is no remedy, the only way is to improve the pretreatment, and ensure that the membrane before the high-pressure pipeline no similar particles fall down, and then replace all the damaged membrane elements.
3. Membrane oxidation: residual chlorine or other oxidizing substances in the influent water of the membrane system exceeds the standard; when cleaning and disinfecting, if it is not carried out in strict accordance with the requirements, the cleaning time or temperature exceeds the standard, resulting in the membrane being oxidized. The way to identify membrane oxidation is to dissect the membrane element and conduct membrane pressure staining test. 4.
4. Leak detection: Conditions such as severely damaged O-rings or ruptured center tubes will result in water ingress or concentrated water seeping into the produced water. Leakage can be identified by disassembling the pressure vessel and removing the membrane elements for inspection.
5. Physical Damage: If one or more membrane elements in one or more pressure vessels are found to be defective, the most likely cause is mechanical damage, such as scratched membrane surfaces, cracked adhesive threads, cracked bonding of the produced water separator to the center tube, and damaged O-rings. These physical damage can be determined by staining experiments.
6. Chemical scaling: Physical contamination usually occurs in the top membrane, while chemical scaling generally occurs in the last membrane. If the membrane element is harmed by chemicals, such as residual chlorine, an increase in salt permeability and an increase in water production may occur.
7. Center Pipe Test Method: The “Center Pipe Test Method” can be used to identify which membrane element is present in any pipe with an obvious problem. The test consists of inserting a hose into the center tube of the spiral wound element up to the end of the pressure tube and then slowly pulling it out to obtain a sample for analysis.
8. Calcium Carbonate Scale Detection: Early detection of calcium carbonate scale is essential to prevent damage to the membrane element from crystals deposited on the surface of the membrane layer. Early detection of calcium carbonate scale can be removed by lowering the pH of the feed water to 3~5 and running for 1~2 hours.
9. Membrane analysis test: dissect the membrane element, and membrane analysis test, can identify the back pressure of the produced water is the method of dissecting the membrane element, and membrane analysis test.
How to optimize the pretreatment process of the reverse osmosis system to reduce pressure drop and increase the desalination rate?
1. Optimize the sequence of pretreatment processes: According to the reverse osmosis pretreatment system includes sand filtration, ultrafiltration, carbon filtration, softening, fine filtration, sterilization and other processes. The order of these processes need to be optimized design to ensure that the processes can be effectively connected, reduce pressure drop, improve overall efficiency.
2. the use of new coagulation - ultra-microfiltration process: new coagulation - ultra-microfiltration process to replace the traditional coagulation - sand filtration process, the use of 20 ~ 100 μm precision stacked filters (or disc filters), which helps to improve the pretreatment effect, reduce the subsequent reverse osmosis membrane contamination, thereby reducing the pressure drop.
3. Control the pH value of the feed water: In the reverse osmosis feed water injection of alkali is used to improve the pH value, the general use of alkali agent is sodium hydroxide (NaOH). Control the pH value of feed water in a certain range, can reduce membrane corrosion, extend the service life of the membrane, but also help to improve the rate of desalination.
4. Adopt dual media filter-ultrafiltration-reverse osmosis combination: dual media filter-ultrafiltration-reverse osmosis as a complete set of pretreatment process in the front end of the positive bed, which can reduce the impact of variable water quality of the water source and can reduce the frequency of regeneration, so as to improve the flexibility and reliability of the operation of the device.
5. Use of seven-core membrane instead of six-core membrane: The reverse osmosis membrane module adopts a one-stage, two-stage arrangement, while replacing the common six-core membrane with a seven-core membrane to ensure that the recovery rate is stable at not less than 75%. This helps to improve the desalination rate and system stability.
6. Simplified reverse osmosis system configuration: It is mentioned that the short-flow reverse osmosis system simplifies the process flow of the reverse osmosis system by eliminating some of the functionally repetitive process units within the reverse osmosis system, reducing the complexity, saving equipment procurement and installation time, and lowering the initial investment budget of the project construction, as well as the occupied land.
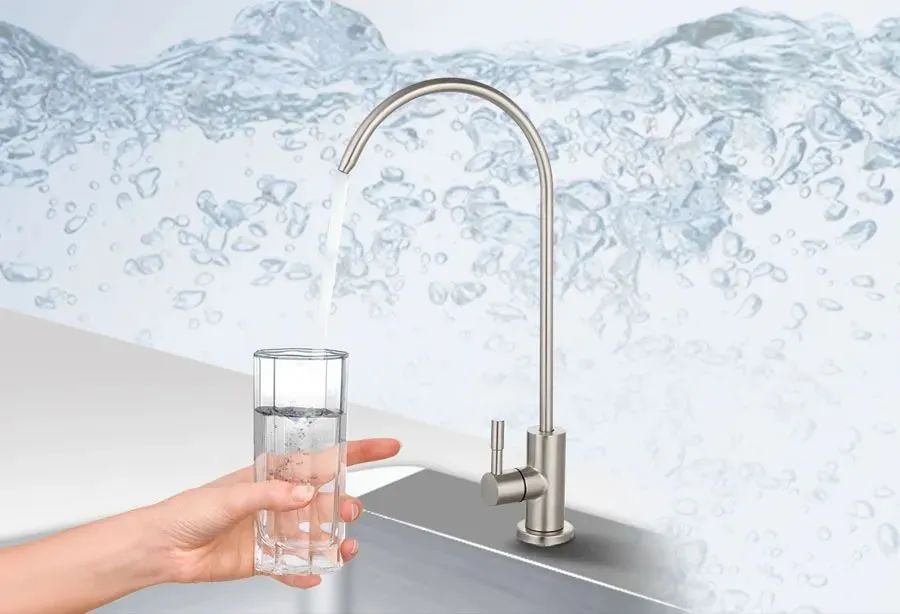
What are the best practices for reverse osmosis system maintenance and instrument calibration?
1. Meter calibration:
- All meters and gauges must be calibrated according to the manufacturer's recommended methods and intervals, usually at least every three months.
- Parameters such as flow, pressure, temperature, and conductivity are recommended to be calibrated once per shift; SDI (feedwater contamination index) is once per shift for surface water and may be once per week for groundwater.
2. Record operating data:
- Record the performance characteristics of the reverse osmosis (RO) unit, including initial data such as flow charts, unit diagrams, pre-treatment, RO unit and post-treatment.
- Collect operational data such as flow rate, pressure, temperature, pH, conductivity/TDS, SDI, etc. throughout the RO service life to evaluate RO unit performance.
3. system fault judgment and troubleshooting:
- If the measured performance of the system does not approach the predicted performance of the software, it is necessary to check whether all the instruments have been calibrated and to confirm whether the system has entered the operation and performance stabilization period.
- When there is a permeate flux, feed water pressure, differential pressure change or desalination rate drop, etc., chemical cleaning should be carried out, and record the relevant parameters.
4. Daily operation management:
- Correct operation and maintenance management is the key to ensure long-term high performance and stable operation of RO membrane system, including the first commissioning of the system and daily start and stop operation.
- Must keep operating records and standardized data processing, in order to grasp the actual performance of the system in a timely manner, and take corrective measures immediately if necessary.
5. Equipment maintenance:
- Regularly clean and overhaul all kinds of equipment, such as quartz sand, activated carbon, positive resin column, etc., to ensure their normal operation.
- Reverse osmosis unit for water conductivity checks, found abnormalities, then repair or replace the relevant components.
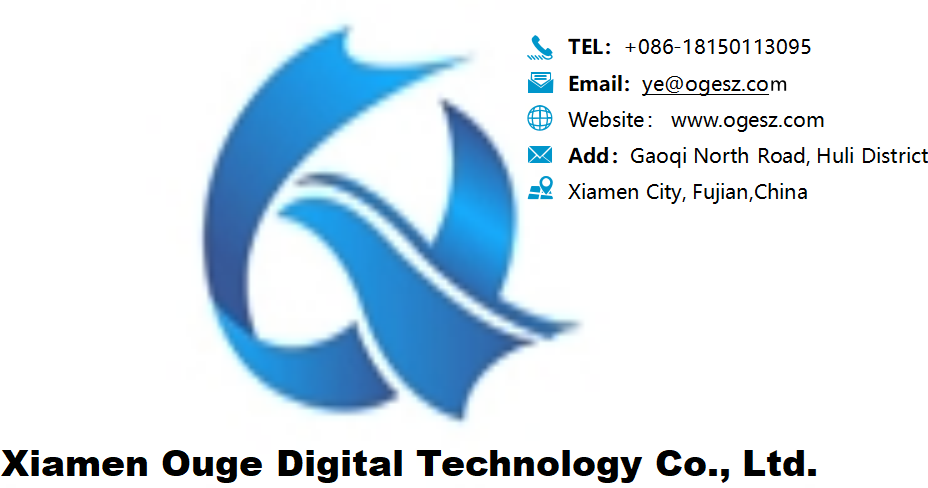