Reverse osmosis feed water quality requirements
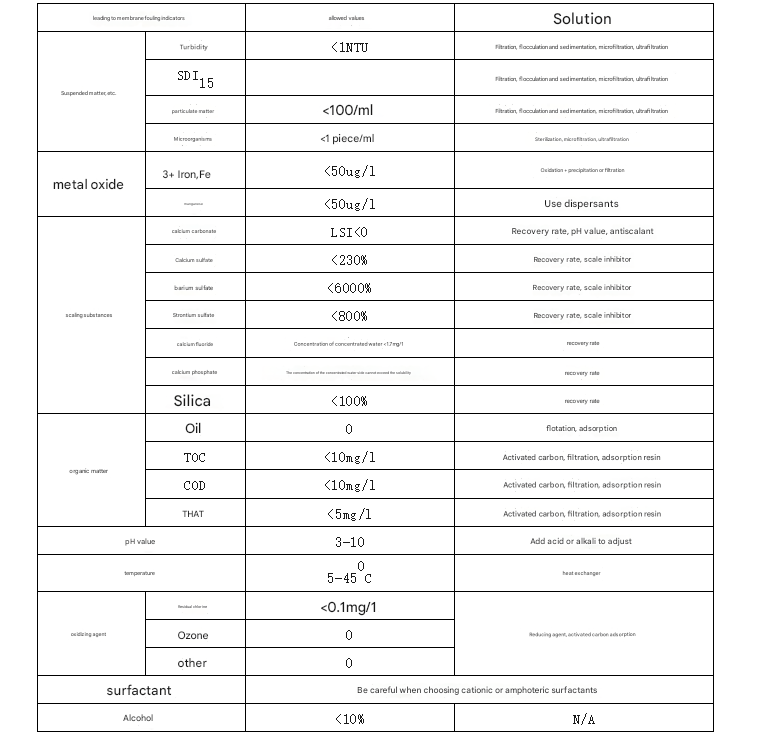
Methods of Pretreatment
Removal of colloids and particulate matter
1 Media Filtration
A common method of removing suspended solids from water is multi-media filtration. Multi-media filters are based on beds of layered anthracite, quartz sand, finely crushed garnet or other materials. The top layer of the bed consists of light and coarse grade materials, while the heaviest and finest grade materials are placed at the bottom of the bed. The principle is filtration by depth - the larger particles in the water are removed in the top layer and the smaller particles are removed deeper in the filter media.
Since colloidal suspensions are both very small and due to repulsion between media charges, filtration alone does not work. In these cases, a flocculant or flocculating chemical must be added prior to filtration. Commonly used flocculants are ferric chloride, alum and PAC.
2 Micro flocculation
If the colloids in the raw water are flocculated or coagulated before filtration, the efficiency of the media filter can be substantially improved, so that the SDI of the effluent water is reduced to about 5. Iron sulfate and ferric chloride can be used to destabilize the negative charge on the surface of the colloid, capturing the colloid onto the new ecological iron hydroxide micro flocs, the use of aluminum-containing flocculants its principle is similar, but because of its potential for residual aluminum ion contamination problems, and is not recommended, unless the use of polymer polymerization of aluminum.
Rapid dispersion and mixing of flocculants is very important, it is recommended to use static mixer or injection point is located in the suction section of the booster pump, usually the optimal dosage of 10-30mg / L, but should be determined for specific projects dosage.
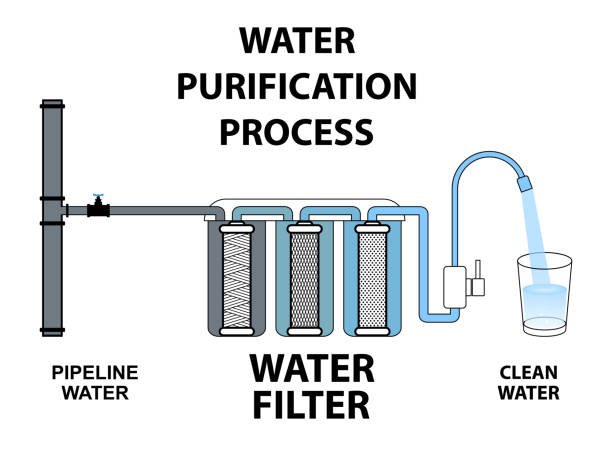
3 Dechlorination chemicals - to eliminate residual chlorine
RO and NF feed water free chlorine should be reduced to less than 0.05ppm in order to meet the requirements of polyamide composite membrane. There are two pretreatment methods for dechlorination, granular activated carbon adsorption and the use of reducing agents such as sodium sulfite. Activated carbon filters are generally used in small systems (50-100gpm) where the investment cost is reasonable. It is recommended to use acid-washed treated high quality activated carbon to remove hardness and metal ions, and the content of fine powder should be very low, otherwise it will cause contamination of the membrane. Newly installed carbon filter media must be fully drenched until the carbon powder is completely removed, usually a few hours or even a few days. We cannot rely on 5μm security filters to protect the reverse osmosis membrane from carbon powder contamination.
The advantage of a carbon filter is that it removes the organic matter that can cause membrane contamination and is more reliable for all feed water treatments than the addition of pharmaceuticals. However, the disadvantage is that carbon becomes a feed for microorganisms that breed bacteria in carbon filters, which results in biological contamination of the RO membrane.
4 Softening pretreatment
Raw water contains excessive scaling cations, such as Ca2+, Ba2+ and Sr2+, etc., need to be softened pretreatment. Softening treatment methods include lime softening and resin softening. Resin softening using sodium ion replacement to remove scaling cations, such as Ca2 +, Ba2 +, Sr2 +, resin exchange after saturation with brine regeneration.
Sodium ion softening method is widely used in atmospheric pressure boiler water treatment. The disadvantage of this treatment method is the high salt consumption, increased operating costs, in addition to the problem of wastewater discharge.
5 microfiltration / ultrafiltration
The reverse osmosis system using ultrafiltration / microfiltration pretreatment process is called integrated membrane system (IMS). The IMS design has some distinct advantages over reverse osmosis systems using traditional pretreatment processes.
● Better MF/UF permeate water quality. lower SDI and turbidity, significantly lower colloidal and organic, microbial contaminant load to the RO.
● The high quality of the MF/UF filtrate can be stabilized because the membrane is an absolute barrier to contaminants here. This stability remains unchanged even for water sources with unusually frequent fluctuations in water quality, such as surface water and wastewater.
● The cleaning frequency of the reverse osmosis system is significantly reduced due to reduced colloidal contamination.
● MF/UF systems are easier and less time consuming to operate than some conventional filtration processes.
● Disposal of MF/UF concentrate waste streams is easier than conventional processes that utilize large quantities of chemicals.
● Smaller footprint, sometimes as little as 1/5 the size of conventional processes in some large systems.
● Facilitates system expansion to increase capacity.MF/UF Membrane CharacteristicsMarketed microfiltration membranes typically have pore sizes of 0.1-20 um.Ultrafiltration membranes used for reverse osmosis pretreatment typically have cut molecular weights in the range of 20,000 to 750,000 Daltons (0.002-0.05 mm).MF/UF membranes can also be used in a wide variety of applications, such as in the production of water, in the production of water, in the production of water, and in the production of water. Common operating transmembrane pressure differentials (TMP) are in the range of 3-30 psi.
Membrane materials are available in polysulfone, polyolefin, polyethersulfone, polypropylene, cellulose-based and other proprietary formulations. Most membrane materials have a fairly wide pH range to facilitate chemical cleaning at low and high pH conditions. Most membranes are also resistant to free chlorine, allowing for periodic or continuous disinfection treatments. The maximum operating temperature for polymer membranes is 40°C, but ceramic membranes can be used at higher temperatures.MF/UF membranes are available in a number of configurations: rolled flat membranes, tubular, hollow fiber, and plate and frame.
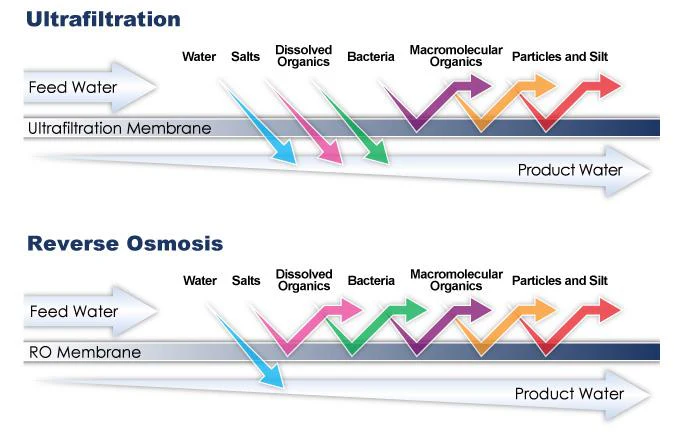
The more common types used for RO pre-treatment are hollow fiber and rolled, mainly due to considerations of investment, energy consumption, contamination resistance, and flux recovery performance in the event of flushing and chemical cleaning.MF/UF membranes are available in two different modes of operation: full volume filtration and staggered flow filtration. The full-volume filtration mode of operation (also called dead-end filtration) is similar to cartridge filters in that there is only feed and filtrate flow (no concentrate flow).
6 Security Filters
All RO/NF units are equipped with cartridge security filters, which are required to have a pore size of at least 10 µm. The security filter is a protective device for the membranes and the high pressure pump, preventing damage caused by possible particles and is the last pretreatment procedure. It is recommended that the pore size of the security filter be no larger than 5 um. When the concentration of silicon in the concentrated water is oversaturated, it is advisable to use a 1 um cartridge to reduce the interaction of silicon with iron and aluminum colloids.
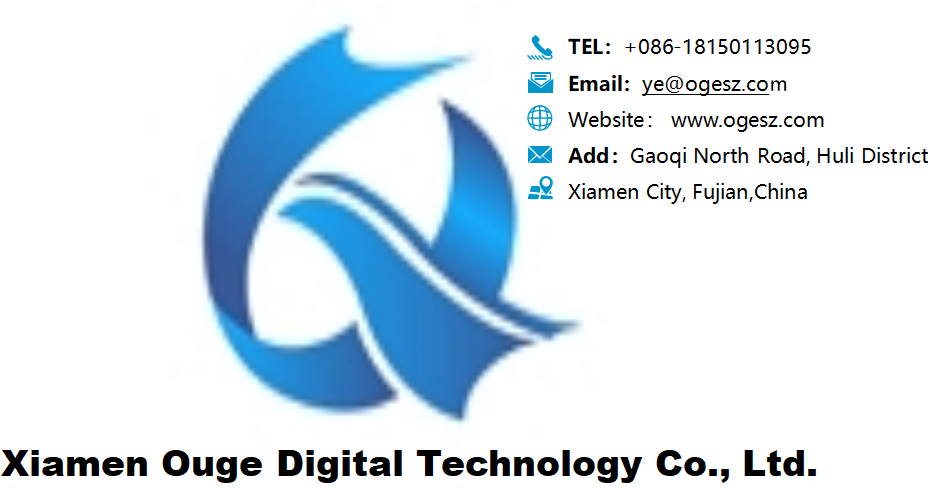