Hello, everyone! Recently, a lot of water treatment partners and I complained that the reverse osmosis equipment with power consumption is amazing, every month only the electricity bill will be heartbroken hair. Don't worry, today I'll share with you an “old engineers personally taught secret” - how to make simple adjustments, so that your reverse osmosis equipment power consumption directly save 45%! This is a treasure of internal experience, not only can help you save costs, but also enhance the efficiency of the equipment, a multi-purpose!
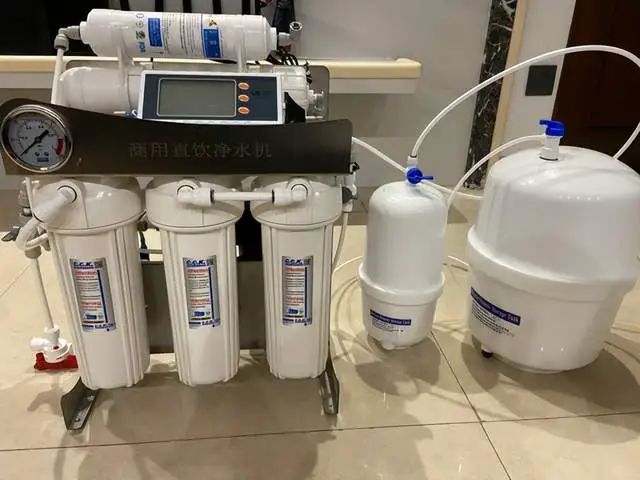
Why do you say reverse osmosis equipment “eat electricity like water”? Before talking about the solution, let's first figure out the problem. The reason why reverse osmosis equipment consumes a lot of electricity, mainly because it requires a high-pressure pump to provide strong pressure, the impurities in the water and salt through the membrane separation out. This high-pressure mode of operation, although the effect is outstanding, but also doomed to its extremely high demand for electricity. So how do these “wildcards” actually reduce energy consumption? Read on!
Operation Tip 1: Optimize water pre-treatment
Many people ignore the importance of pretreatment, in fact, the better the quality of feed water, reverse osmosis membrane work to overcome the resistance is smaller, which means that the pressure demand is reduced, and power consumption is reduced. **Skill point: ** in the pre-treatment by adding an automatic flushing device or replacement of more efficient filter media, you can significantly reduce the burden of subsequent equipment.
Operation Tip 2: Precise control of operating pressure
Don't think that higher pressure is better! Excessive pressure will not only accelerate the membrane damage, but also let the pump overloaded for a long time, resulting in a surge in power consumption. **Skill point: ** according to the actual water intake, in the set range of reasonably low pressure, such as from the original 10MPa to 8 ~ 9MPa, you can significantly save power.
Operation Tip 3: Regular cleaning of the membrane module
When the membrane module is contaminated and clogged, more energy is needed to maintain normal operation. So regular cleaning can not only keep the water effect, but also make the whole system easier to “breathe”. **Skill point: ** every 3 to 6 months for a chemical cleaning, and according to the water intake to determine whether the cycle needs to be shortened.
Operation Tip 4: Installation of frequency converter control system
Traditional constant-speed pumps keep a fixed speed all the time, while frequency converters can dynamically adjust the pump speed according to the actual flow demand, thus avoiding unnecessary power waste. Installation once, long-term benefits! **Skill point: **Choose a frequency converter suitable for the power range of your model, and look for professionals to debug to ensure the best energy-saving effect.
Operation Tip 5: Recovery of concentrated water residual pressure
The old engineers mentioned the big killer to come! In fact, concentrated water still remains a large number of unreleased pressure, if the installation of energy recovery devices, these residual pressure can be reused to drive other links, thus indirectly saving electricity. **Skill point: ** There is a special RO system on the market for the “PX device”, although the investment is slightly larger, but a few months to save the cost of the cost can be earned back!
Operation Tip 6: “staggered electricity consumption” to avoid peak times
If your business happens to use the peak and valley time pricing, then stagger the peak hours of electricity to run the machine, is the most simple and brutal but very effective way to do it! **Skill point: **Arrange to start the mainframe at night or during the low hours, and record the daily operating data for further optimization.
Operation Tip 7: “small horse-drawn cart” configuration upgrades
The last method for those who are still chewing on the old model. If you find that your pumps, piping or other components are not up to the standards of today's new technology, it may be time to consider a complete upgrade. A hardware revolution to bring cost reduction and efficiency, not a little bit oh ~ **Tips pointing: **Prioritize the replacement of inefficient high-power pumps, and then gradually replace the obsolete piping and valves and other wear parts.
The above 7 operations, not just online search can find tips, each of which are cohesive old engineers for many years to summarize the first-hand experience. If you are for the high cost of factory operations and headaches, you may wish to start from these methods to try it ~ of course, the “wild way” also pay attention to the local conditions, you can combine their actual situation to choose a few of these items to implement, I believe that there will be an immediate effect. If you think this article is helpful to you, please like the favorites favorites support ah ~ we'll see you next time ~!
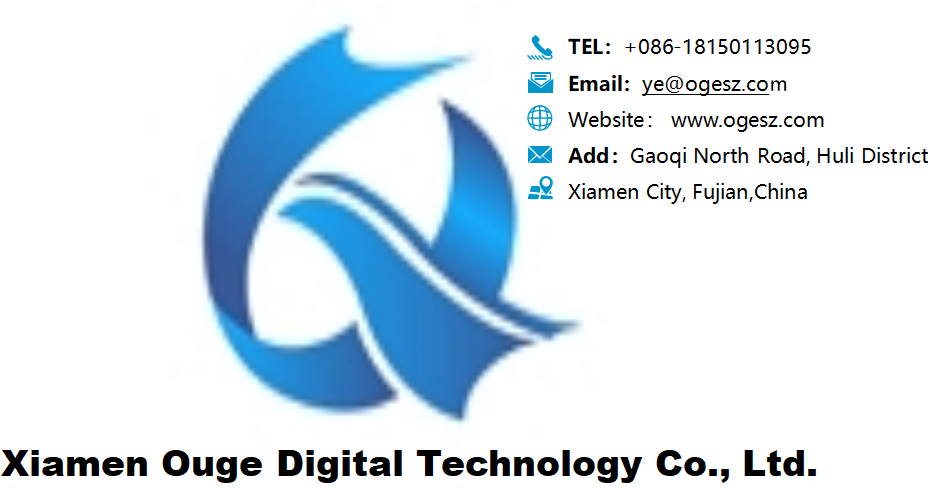