1. Reverse osmosis membrane contamination causes
1.1 reverse osmosis membrane membrane performance damage, and cause membrane contamination
1, polyester material reinforced nonwoven fabric, about 120μm thick;
2, polysulfone material porous intermediate support layer, about 40μm thick;
3, polyamide material ultra-thin separation layer, about 0.2μm thick. According to its performance structure, such as osmosis membrane membrane performance damage may have the following reasons:
1, the new reverse osmosis membrane maintenance is not standardized;
2, maintenance in line with the requirements, storage time exceeds 1 year;
3, out of service state, reverse osmosis membrane maintenance is not standardized;
4, the ambient temperature is below 5 ℃;
5, the system is running under high pressure;
6, improper operation when shutting down.
1.2 Frequent changes in water quality caused by membrane contamination
Raw water quality with the design of the water quality has changed, so that the pretreatment load increased due to inorganic matter in the water, organic matter, microorganisms, particulate matter and colloids and other impurities increased, so the membrane contamination chances increase.
1.3 Cleaning is not timely and incorrect cleaning methods caused by membrane contamination
In the process of use, the membrane in addition to the performance of the normal attenuation, cleaning is not timely and incorrect cleaning method is also an important factor leading to serious membrane contamination.
1.4 Not correctly add agents composite polyamide membrane in use, because the polyamide membrane residual chlorine resistance is poor, in the use of chlorine and other disinfectants are not correctly added, coupled with the user of microbial prevention of insufficient attention to microbial contamination is likely to lead to.
1.5 Membrane surface wear membrane element is blocked by foreign matter or membrane surface wear (such as sand, etc.), this situation should use the detection method to detect the elements in the system, find the damaged elements, transform pretreatment, replace the membrane element
2. Phenomenon of reverse osmosis membrane contamination
In the reverse osmosis operation process, due to the selective permeability of the membrane, so that some solutes in the membrane surface near the accumulation, thus occurring membrane fouling phenomenon. Common signs of fouling are as follows:
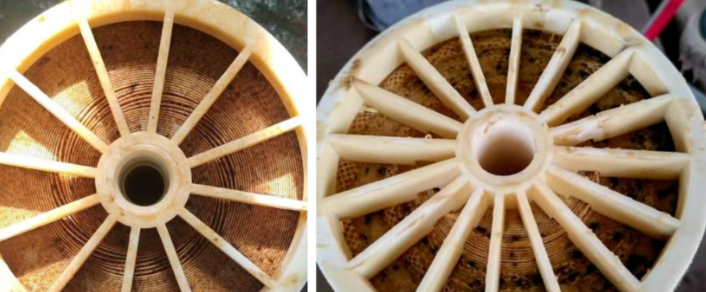
One is biological fouling (symptoms appear gradually) organic deposits are mainly live or dead microorganisms, hydrocarbon derivatives, natural organic polymers and all carbon-containing substances. Initial manifestations are increased desalination rate, increased pressure drop and reduced water production. Then there is colloidal fouling (symptoms appear gradually) membrane separation process, the concentration of metal ions and changes in solution pH may be metal hydroxide (mainly represented by Fe (OH) 3) deposits, resulting in fouling. Initially manifested as a slight reduction in the desalination rate, and gradually increased, and finally the pressure drop increased and water production decreased. There is also particulate matter fouling reverse osmosis system in the operation process, if the security filter problems, will lead to particulate matter into the system, resulting in membrane particulate matter fouling. The initial performance of the concentrated water flow rate increases, the desalination rate in the initial change is not large, the water production gradually decreased, the system pressure drop rises very quickly. The last common and chemical scaling (symptoms appear soon) when the feed water contains high Ca2+, Mg2+, HCO3-, CO32-, SO42- and other ions, it will produce CaCO3, CaSO4, MgCO3 and other scale deposited on the membrane surface. It is manifested by a decrease in the desalination rate, especially in the last section is very obvious, as well as a decrease in water production. Membrane contamination is the main reason for the decline in membrane permeate flux. Including the membrane pore and macromolecular solute blockage caused by membrane filtration resistance increases; solute adsorption on the inner wall of the pore; the formation of a gel layer on the membrane surface to increase the mass transfer resistance. Component deposition in the membrane pore, will cause the membrane pore reduction or even blockage, actually reducing the effective area of the membrane. The additional resistance generated by the contamination layer formed by the deposition of components on the membrane surface may be much greater than the resistance of the membrane itself, while making the permeate flux independent of the permeability of the membrane itself [25]. This effect is irreversible, the degree of contamination with the membrane materials, solvents in the retention solution and the concentration of macromolecular solutes, the nature of the solution, pH, ionic strength, charge composition, temperature and operating pressure, etc., contamination is serious can make the membrane flux decreased by more than 80%. In the operation of the system, the membrane contamination is a very difficult problem, its emergence caused by the reverse osmosis device removal rate and water permeability, membrane flux of a substantial decline, while increasing the operating pressure of the various segments, prompted by the operation and operation costs rise, seriously affecting the service life of the membrane and reverse osmosis technology development and utilization.
3 Solutions
3.1 Improve the pretreatment
For each set of membrane device, people want it to maximize the role, hope to have the highest desalination rate, the maximum amount of water permeability and as long as possible life, to achieve the above three points, the water supply quality is crucial, so the raw water into the membrane device must have good pretreatment. Reasonable pretreatment is very important to the long-term safe operation of the reverse osmosis device. With the pretreatment to meet the requirements of reverse osmosis feed water quality, you can ensure that the flow of produced water to maintain a stable; desalination rate maintained at a certain value for a long time; product water recovery can be unchanged; operating costs to reach a minimum; membrane service life is longer and so on. Specifically, reverse osmosis pretreatment is to do:
(1) prevent pollution on the membrane surface, that is, to prevent suspended impurities, microorganisms, colloidal substances, etc. attached to the membrane surface or fouling the membrane element water flow channel.
(2) Prevent scaling on the membrane surface. During the operation of the reverse osmosis unit, due to the concentration of water, there are some insoluble salts deposited on the membrane surface, so it is necessary to prevent the generation of these insoluble salts.
(3) Ensure that the membrane is protected from mechanical and chemical damage so that the membrane has good performance and a long enough service time.
3.2 Cleaning of the membrane
Although the material liquid after a variety of pretreatment measures, long-term use of the membrane surface may also produce deposits and scaling, so that the membrane pore blockage, water production decreased, so the pollution of the membrane is necessary to carry out regular cleaning. But the reverse osmosis membrane system can not wait until after the pollution is very serious to clean, this will increase the difficulty of cleaning, but also to increase the cleaning steps and cleaning time extension. To correctly grasp the timing of cleaning, timely removal of dirt. Cleaning principles: understanding of local water quality characteristics, chemical analysis of contaminants, through the results of the analysis, to select the best cleaning agent and cleaning method, to find the best method for specific water supply conditions to provide a basis for; cleaning conditions: a. Product water volume than the normal decline of 5% -10%. b. In order to keep the correct amount of product water, the corrected temperature of the water supply after the pressure increase of 10% -15%. c. Transmission of the conductivity of the water quality (Salt content increased) increased by 5% -10%. d. Multi-section RO system, through the different sections of the pressure drop significantly increased. Cleaning methods: first system backwash; then negative pressure cleaning; mechanical cleaning if necessary; then chemical cleaning; conditions can be ultrasonic cleaning; online electric field cleaning is a very good method, they are expensive; due to the chemical cleaning effect is relatively good, the rest of the method is not easy to achieve some, and the suppliers to provide the agents, although the name and method of use is not the same, but the principle is generally the same! The principle is more or less the same. Such as my company is now using membrane cleaner MC2, MA10. cleaning steps are as follows: cleaning single-segment system: (1) configuration of cleaning fluid; (2) low-flow input cleaning fluid; (3) circulation; (4) immersion; (5) high-flow pump circulation; (6) flushing; (7) restart the system. For special pollutants cleaning are: cleaning sulfate scale, cleaning carbonate scale, cleaning iron and manganese pollution, cleaning organic pollution.
3.3 Proper Maintenance of Membranes
Maintenance of new reverse osmosis membranes New reverse osmosis membrane elements are usually impregnated with 1% NaHSO3 and 18% glycerol aqueous solution and stored in sealed plastic bags. In the case of the plastic bag is not broken, storage for about 1 year, will not affect its life and performance. When the plastic bag is opened, it should be used as soon as possible to avoid adverse effects on the components due to oxidation of NaHSO3 in the air. Therefore the membrane should be opened before use as much as possible. During the non-production period, the maintenance of the reverse osmosis system is a more important issue. Can be carried out according to the following methods.
1, the system is out of operation for a short period of time (1-3 days): before the shutdown, the system is first low-pressure (0.2-0.4MPa), high-flow (about equal to the system's water production) flushing, for 14-16 minutes; maintain the usual natural water flow, so that the water flows into the thick waterway.
2、System shutdown for more than a week (ambient temperature above 5 ℃): before shutdown, first of all, low-pressure system (0.2-0.4MPa), large flow (about equal to the system's water production) flushing, time 14 ~ 16 minutes; in accordance with the reverse osmosis system operating instructions about the system's chemical cleaning method of chemical cleaning; chemical cleaning is complete, rinse the reverse osmosis membrane; preparation of 0.5% of the Formalin solution, low-pressure input system, cycle for 10 minutes; close all system valves, sealing; if the system is out of operation for more than 10 days, the formalin solution must be replaced every 10 days.
3, the ambient temperature below 5 ℃: before shutdown, the system for low-pressure (0.2-0.4MPa), high-flow (about equal to the system's water production) flushing, time for 14 ~ 16 minutes; in the conditions of the place, you can raise the ambient temperature to 5 ℃ or more, and then in accordance with the method of 1, the system maintenance; if there are no conditions for the ambient temperature to be raised, then: low-pressure (0.1MPa), the flow rate is 1.0MPa, the flow rate of the system's water production. Flow rate of 1/3 of the system's water production for a long flow of water to prevent the reverse osmosis membrane is frozen, and to ensure that the system is running for 2 hours a day; in accordance with the methods of 2) and 3) in 1, after cleaning the reverse osmosis membrane, the reverse osmosis membrane is removed, moved to the ambient temperature is greater than 5 ℃, immersed in the preparation of 0.5% formalin solution, every two days to turn over the system piping, the water should be drained clean to prevent damage to the system due to icing.
3.4 Avoid membrane operation under high pressure
Residual gas is retained when the system is started and stopped, causing the system to operate under high pressure. The pressure gauges before and after the filter in the system are used to monitor the pressure drop of the cartridge, and the primary and final pressure gauges are used to monitor the pressure drop of the RO membrane module. The influent and concentrate valves are adjusted to ensure operating pressure and recovery. If the operation of the produced water flow or total flow drop, or primary and intermediate pressure difference than the initial operation of the pressure difference increased by a large amount (to the initial operation of the new reverse osmosis membrane module data as a standard), it is necessary to flush or clean the system to ensure that the performance of the membrane module safety all. 1, after the evacuation of the equipment, re-run, the gas did not exhaust the rapid boosting of pressure to run. Should be under the pressure of the system will be the remaining air exhaust, and then gradually increase the pressure to run. 2, in the pretreatment equipment and high-pressure pumps between the joints of bad sealing or leakage (especially micron filter and its pipeline leakage) when the pretreatment water supply is not sufficient, such as micron filter clogging, in the sealing of the place due to the vacuum will be part of the air will be sucked in. The micron filter should be cleaned or replaced to ensure that the pipeline does not leak.3. Whether the operation of each running pump is normal, whether the flow rate is the same as the specified value, and compare with the pump operating curve to determine the operating pressure.
3.5 Pay attention to the operation when shutting down
1, shutdown when the rapid depressurization did not carry out a thorough flushing. As the concentration of inorganic salts in the concentrated water side of the membrane is higher than that of the raw water, it is easy to scale and contaminate the membrane. When preparing for shutdown, gradually lower the pressure to about 3 bar and flush with pre-treated water for 14 to 16 minutes.
2, in preparation for shutdown, add chemical reagents, will make the agent retained in the membrane and membrane shell, causing membrane contamination, affecting the service life of the membrane. The addition should be stopped.
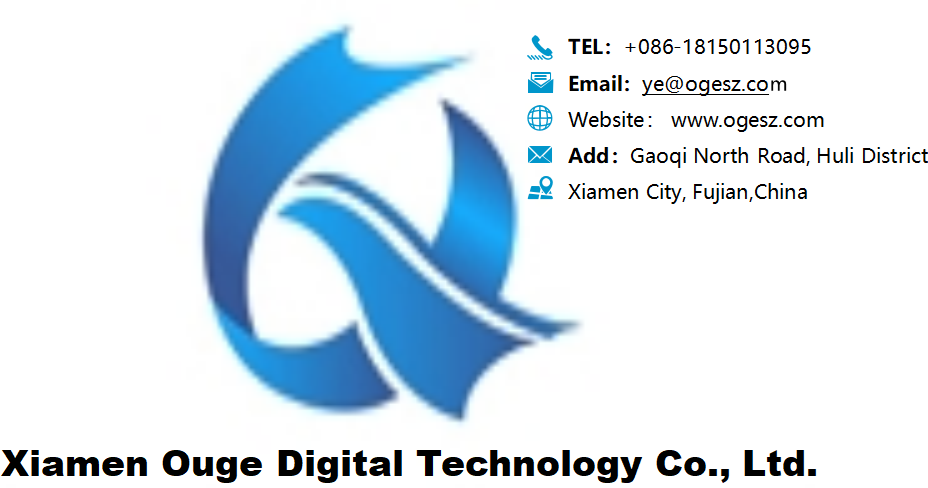